The Future of Manufacturing: Inside the Plastic Industrial Blade Factory
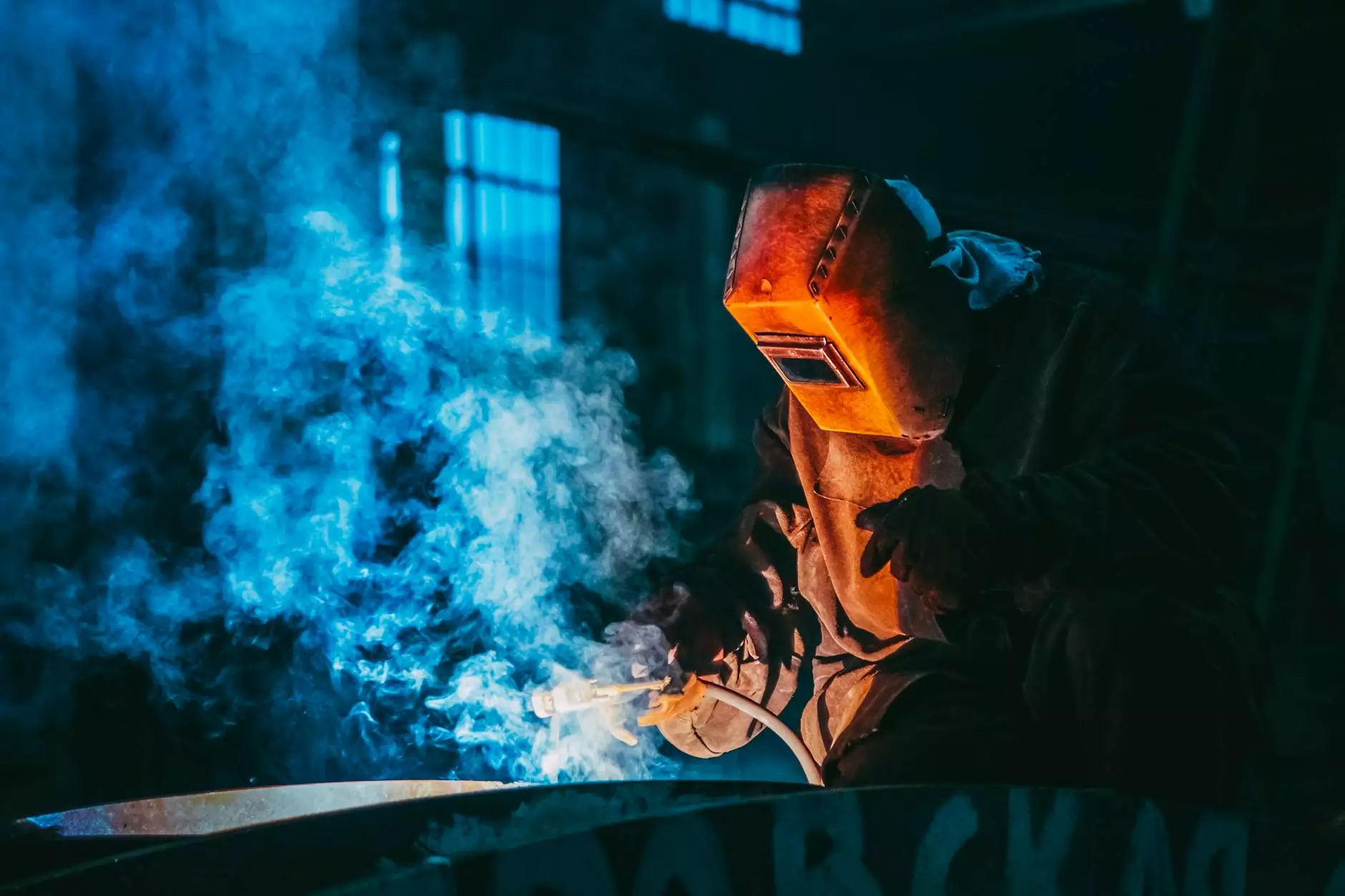
In today's competitive landscape, the manufacturing industry continuously evolves, and one of the most fascinating sectors is the plastic industrial blade factory. These factories are at the forefront of innovation, producing high-quality plastic blades that serve a wide range of applications across various industries, from packaging to healthcare.
Understanding Plastic Industrial Blades
Plastic industrial blades are specialized cutting tools made from high-performance plastic materials. Unlike traditional metal knives, these blades are characterized by their lightweight nature and resistance to corrosion, making them ideal for specific applications.
The Benefits of Plastic Industrial Blades
- Corrosion Resistance: Unlike metal blades, plastic blades do not rust or corrode, ensuring longevity and reliability in various environments.
- Lightweight: The lightweight quality of plastic blades reduces fatigue during prolonged use, leading to higher efficiency.
- Versatility: Plastic blades can be used in numerous sectors, including food processing, packaging, and textiles.
- Cost-Effectiveness: Producing plastic blades often incurs lower costs than metal counterparts, making them more affordable for manufacturers.
- Safety: Plastic blades tend to be safer to handle than sharp metal blades, reducing the risk of injuries.
The Manufacturing Process of Plastic Industrial Blades
The manufacturing process of plastic industrial blades is a detailed and meticulous procedure that encompasses several stages to ensure high-quality outcomes.
1. Material Selection
The journey of a plastic blade begins with the selection of materials. Commonly used plastics include:
- Polypropylene: Known for its strength and flexibility.
- Polyethylene: Offers excellent impact resistance.
- Nylon: Provides superior wear resistance and durability.
2. Molding and Shaping
The selected plastic is then heated and molded into the desired blade shapes using advanced injection molding techniques. This process ensures precision and consistency in the manufacturing of each blade.
3. Finishing
After molding, the blades undergo finishing processes, which may include grinding and polishing. These steps enhance the cutting edges of the blades, ensuring they meet industry standards for sharpness and durability.
Importance of Quality Control in Plastic Blade Manufacturing
Quality control is paramount in a plastic industrial blade factory. Rigorous inspection protocols are implemented to ensure that every blade produced meets strict specifications. This is not only vital for customer satisfaction but also essential for compliance with regulatory standards.
Quality Assurance Processes
The following are critical components of the quality assurance processes:
- Material Testing: Testing raw materials before production to ensure they meet the required specifications.
- In-Process Inspections: Regular checks throughout the manufacturing stages to catch any defects early.
- Final Product Testing: Each batch of blades is tested for performance, including sharpness, durability, and safety features.
Knife Sharpening Services: Enhancing Blade Longevity
A critical aspect in the lifecycle of plastic industrial blades is knife sharpening services. These services are essential for maintaining the efficiency and effectiveness of the blades.
Why Knife Sharpening Matters
Sharpening is crucial for several reasons:
- Performance: A sharp blade performs better, allowing for cleaner and more precise cuts.
- Cost Efficiency: Regular sharpening extends the lifespan of blades, reducing replacement costs for manufacturers.
- Safety: Dull blades can lead to accidents as more force is needed to achieve the same cut, increasing the risk of slips and injuries.
Professional Knife Sharpening Services
Utilizing a professional service for sharpening ensures that blades receive expert care. This can include:
- Precision Techniques: Professionals use specialized equipment and techniques tailored for various blade types and materials.
- Assessment: Along with sharpening, a thorough assessment of the blade's condition can provide insight into potential replacements.
The Role of Technology in Blade Manufacturing
As technology advances, so does the manufacturing process of plastic blades. The integration of cutting-edge technology enhances efficiency and product quality.
Automation in Production
Many factories have embraced automation, leading to decreased production times and minimized human error. Automated systems can help:
- Streamline Processes: Automated machines can take over repetitive tasks, allowing skilled workers to focus on complex operations.
- Increase Output: Automated systems can operate continuously, significantly boosting production capacity.
Advanced Quality Monitoring
The implementation of real-time monitoring systems ensures that every production phase is scrutinized. These systems can detect variances in the manufacturing process, prompting immediate corrective actions.
Market Trends Impacting the Plastic Industrial Blade Industry
The demand for plastic industrial blades is influenced by market trends that shape their production and application.
1. Sustainability Efforts
With a growing awareness of environmental issues, many manufacturers are prioritizing sustainability. This includes:
- Recyclable Materials: Utilizing plastics that can be recycled to reduce waste.
- Eco-Friendly Processes: Implementing energy-efficient manufacturing processes.
2. Customization Trends
Many industries are moving toward customized solutions. A plastic industrial blade factory needs to adapt by:
- Offering Tailored Solutions: Being flexible in production to meet specific customer needs.
- Innovating Designs: Collaborating with clients to design blades that serve unique applications.
3. Industry-Specific Demand
Various sectors, like food processing and packaging, are showing increased demands for specialized plastic blades. This requires factories to focus on:
- Product Development: Creating products tailored for specific industries.
- Compliance with Standards: Meeting stringent industry regulations to ensure safety and effectiveness.
Conclusion: The Future of Plastic Industrial Blade Factories
The future of plastic industrial blade factories is bright, bolstered by advancements in technology, sustainability practices, and an unwavering commitment to quality. As businesses worldwide demand more efficient, cost-effective, and eco-friendly solutions, these factories are poised to be at the heart of the manufacturing revolution.
Investing in innovation, adopting ethical business practices, and providing exceptional knife sharpening services will ensure that factories not only thrive but also lead the way in a competitive marketplace.
For more information and to explore professional services, including knife sharpening, visit szblade.com.